
Project Overview
Element Can Racks
Sellafield Nuclear Power Station
Project Overview
The demand for safe and efficient storage of spent nuclear fuel at Sellafield, one of the UK's key nuclear facilities, prompted the need for specialist storage racks. These racks were designed to optimise storage capacity while ensuring safety and compliance with rigorous regulatory standards. Steel Dynamics collaborated with the customer, the primary contractor, to supply the stainless steel components for the construction of 63 element can racks for spent nuclear fuel.
With a commitment to excellence and innovation, Steel Dynamics have established themselves as a trusted partner in complex engineering projects. Working in conjunction with our customer, we processed the steel components to be sent out in kit form for assembly. Additionally, Steel Dynamics undertook the finishing and testing of the assembled parts to ensure compliance with the required specifications and standards.
The storage racks for spent nuclear fuel needed to meet stringent regulatory requirements for safety, durability and environmental protection, necessitating adherence to precise specifications and standards throughout the manufacturing process. Fabricating and assembling the large-scale storage racks also required intricate manufacturing processes and precision engineering to ensure the structural integrity and functionality of the final product.
The Hybrid 2 63 element can rack design (8 tonne, 6 metre high racks to hold 63 cans of spent nuclear fuel) represented a significant advancement in storage capacity and efficiency, enabling Sellafield to safely store all spent Advanced Gas-cooled Reactor (AGR) fuel without the need for new facilities.
Originally some of the parts were designed to be machined from sawn cut rectangular blanks, with a yield of 28 parts per stainless steel plate. As metal processing experts, Steel Dynamics applied our ‘Total Service Concept’ approach aimed at reducing manufacturing processes and cycle times to add value from point of manufacture to the point of use. The outcome was to use our waterjet cutting expertise and innovative nesting software to produce 43 parts per sheet, which is a huge 53% yield increase and substantial project cost savings.
With the need to deliver a significant number of racks over a five-year period, maintaining operational efficiency and meeting production milestones were paramount to the success of the project. We also conducted thorough testing and inspection of the finished components to verify compliance with regulatory standards and client specifications, ensuring the safety and reliability of the storage racks.
Steel Dynamics successfully delivered a cutting-edge storage solution that enhances safety, efficiency and sustainability in nuclear fuel management. The project stands as a testament to the capabilities of UK manufacturers in delivering critical infrastructure projects, with 63 element can racks that not only contributed significant savings in future decommissioning costs, but that also safeguard the environment and support future generations.
Material grade supplied:
Steel quantity supplied:
Process:
Time to market:
Industry:
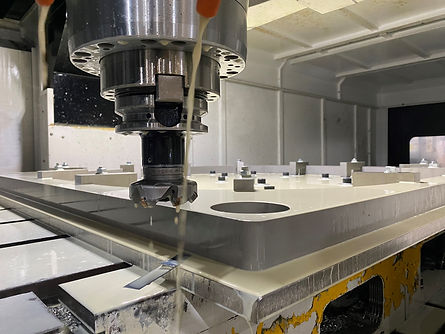

304L & 316L Stainless Steel
120 tonnes (ongoing)
Laser Cutting & Machining
2-3 years
Nuclear
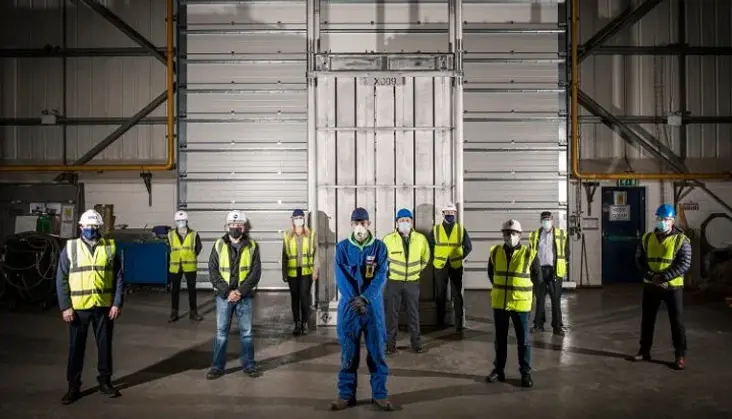
