
Press Braking
Press braking of stainless steel is a highly efficient and versatile method of metal fabrication, capable of producing strong, corrosion-resistant, and aesthetically pleasing parts.
Do you need sheet metal folded up to 4 metres in length? No problem!
With 3 CNC press brake machines, including the powerhouse Bystronic Xpert Pro 320, boasting up to 320 tonnes of force, we're equipped to handle projects of any complexity.
Steel Folding
Press braking is a cold-forming process where a sheet or plate of metal is positioned between a punch and die and then bent by applying force with the press brake. The machine can bend metal at different angles and radii, allowing for the creation of complex shapes and parts. Hydraulic Press Brakes offer precision and the ability to apply controlled pressure over various bending operations.
When working with stainless steel, press brakes can handle a wide range of thicknesses, from thin sheets to thicker plates. The material’s malleability and strength make stainless steel an ideal candidate for press braking, but it also requires special attention to avoid issues such as cracking, distortion, or loss of surface finish.
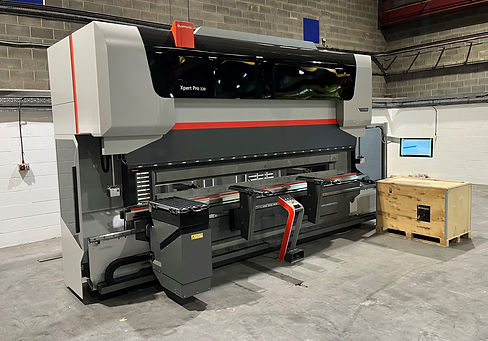

Press Brake Benefits
Modern CNC press brakes allow for highly precise and repeatable bends, making them ideal for stainless steel fabrication, where exact dimensions and tight tolerances are required. Press brakes can create a wide range of shapes and angles in stainless steel, from simple bends to complex geometries. The precision also ensures consistent results.
Press brakes can be configured to handle different types of stainless steel grades, thicknesses, and sizes. With interchangeable tooling, we can adjust the punch and die to produce a wide variety of angles and forms, allowing for fully customised stainless steel parts tailored to specific applications.
Minimal Material Waste
Press braking is a cost-effective process with minimal material waste. Since the process is performed cold, it requires no additional heating or chemical treatments, reducing both energy consumption and material loss. This is especially important when working with high-value materials like stainless steel.
Press braking maintains these properties throughout the process, producing parts that are not only strong and functional but also long-lasting in harsh environments. Furthermore, press braking remains an excellent method for bending stainless steel into precise shapes, and with the right equipment and expertise, any challenges can be effectively managed.
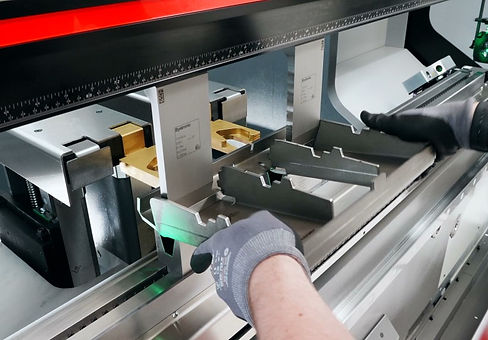
While stainless steel presents challenges such as springback, high strength and work hardening, modern press brakes equipped with advanced CNC technology can deliver precision bending with minimal waste and excellent repeatability.
The ability to form stainless steel into increasingly complex and customised shapes ensures that this method will remain a cornerstone of metal fabrication for years to come.